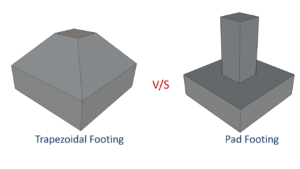
1) Ordinary Portland Cement
This is the most commonly used cement in construction projects worldwide. It’s a versatile cement that can be used in a variety of applications, from general construction to precast concrete products. OPC is known for its strength, durability, and workability, making it suitable for a variety of construction applications. It’s commonly used in the construction of buildings, bridges, roads, and other structures. OPC is versatile and can be used in combination with other materials, such as aggregates, to create different types of concrete mixes.
2) Portland Pozzolana Cement
Portland Pozzolana cement (PPC) is a type of hydraulic cement that’s made by blending Portland cement with pozzolanic materials, such as fly ash or silica fume. The pozzolanic materials improve the workability and durability of the cement, making it suitable for a variety of construction applications. PPC is commonly used in home building construction and mass concrete structures, such as dams and bridges, where durability is a critical factor.
3) Rapid Hardening cement
Rapid-hardening cement is a type of hydraulic cement that’s specially designed to gain strength quickly. Rapid-hardening cement is used in situations where fast-setting concrete is required, such as in the construction of pavements, precast concrete products, and repair work. It has a higher early strength compared to OPC, allowing structures to be put into service faster.
4) Extra Rapid Hardening Cement
Extra Rapid Hardening Cement is a type of hydraulic cement that’s similar to rapid-hardening cement, but it gains strength even faster. It’s made by grinding Ordinary Portland cement clinker with a higher amount of calcium chloride. This combination accelerates the setting time and early strength gain of the cement. Extra rapid-hardening cement is used in situations where fast-setting concrete with high early strength is required, such as in cold weather conditions or emergency repair work. It’s commonly used in the construction of airport runways, industrial floors, and precast concrete products.
5) Quick Setting Cement
Quick-setting cement is a type of hydraulic cement that’s designed to set and harden quickly. It aids time-sensitive projects such as the repair of water pipes, sewers, and tunnels. Its combination of materials accelerates the setting time of the cement, allowing it to reach its initial set in just a few minutes, similar to that of fast setting concrete.
6) Low Heat Cement
Low heat cement is a type of hydraulic cement that’s specially designed to produce less heat during the hydration process. It’s made by reducing the amount of tricalcium aluminate by 6%. This results in slower strength gain and lower heat of hydration, making it ideal for use in large concrete structures that are prone to cracking due to heat buildup. Low-heat cement is commonly used in the construction of dams, nuclear power plants, and large-mass concrete structures.
7) Sulphate Resisting Cement
Sulphate-resisting cement is a type of hydraulic cement that’s designed to resist the damaging effects of sulphate salts present in soil and groundwater. Sulphate-resistant cement is commonly used in construction projects where the soil or groundwater has a high sulphate content, such as in coastal areas, mines, and canal linings, retaining walls.