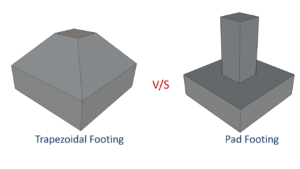
These concrete vibrators are also referred to as poker or immersion vibrator. These are extensively used in building industry. A needle vibrator consists of a cylindrical casing made of steel and is vibrated by means of a flexible drive with an outer tube run from an operating machine which can be run by electricity, petrol, diesel or compresses air. The frequency of vibrations of an immersion vibrator is very important as higher frequency gives better compaction. It varies from 3500 to 12000 cycles per minute. Frequencies below 3500 cycles per minute are inefficient for concrete compaction. The diameter of the vibrating part varies from 20 to 75 mm and its length varies from 25 to 90 cm.
The following points are important for efficient use of needle vibrators.
The amount of concrete that can be vibrated by one vibrator per hour varies from 4 to 30 m3 depending on the vibrator and the method of placing concrete.
Cast iron is manufactured by remelting pig iron with coke and limestone. This remelting is done in a furnace known as cupola furnace, which is more or less same as blast furnace. Its shape is cylindrical with diameter about 1m and height of about 5m. The raw materials are led from the top and the furnace is fired. The impurities of pig iron are removed to some extent by oxidation. The molten cast iron is led into moulds of required shapes to form what are known as cast iron castings and slag is removed from the top of cast iron at regular intervals.
Wrought iron is almost pure and it hardly contains carbon more than 0.15 percent. But the process of its manufacture is laborious and tedious. Wrought iron is manufactured by four operations
It is used for rivets, chains, ornamental iron work, railway couplings, water and steam pipes, bolts and nuts, horse shoe bars, hand rails, straps for timber roof trusses, boiler tubes, roofing sheets etc.
Social Chat is free, download and try it now here!